The power of design sheds light on
traditional Japanese craftsmanship.
Tomita: This time, I’d like to talk about the Seiko Presage Craftsmanship Series. I have been involved with Presage as a designer since 2011. In the Craftsmanship Series, I am in charge of design and communicating with traditional craftsmen to create products that best showcase the appeal of authentic mechanical watches.
Igarashi: From 2013 to 2017, I was involved in this series in charge of product development , overseeing the entire production process until the launch of new Presage products. I was also responsible for technological matters and coordinating between the designer, Tomita-san, and the craftsmen. Many other members involved in exterior design and technology and parts development are also working hard to realize the product, and I am here today as one of team.
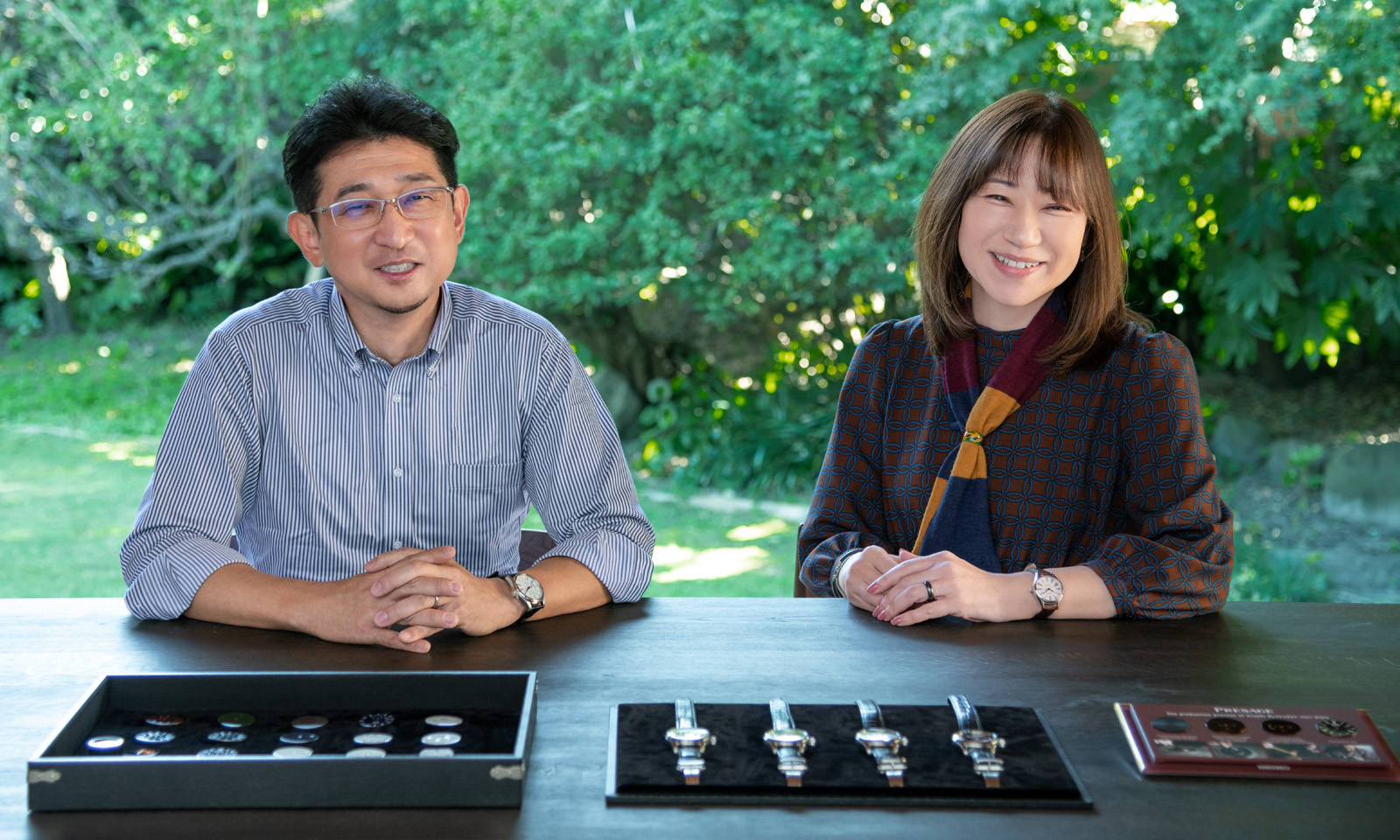
Tomita: The Craftsmanship Series began with a watch planned in 2013 for the 100th anniversary of Seiko Watches. This watch pays homage to the first watch produced in Japan, the Laurel, which was launched in 1913, and is made with enamel, just as it was then. Like the Laurel, we aimed to create a design that shows off materials that will not fade away for a long time.
Igarashi: Mechanical watches can be used for a long time if they are maintained. In that sense, enamel is a great match for them.
Tomita: At that time, even in the Japanese market, where radio controlled, solar watches were at the height of popularity, there was a rapidly growing momentum to cherish traditional Japanese techniques and culture, and customers must have felt a fresh surprise at a mechanical watch made with enamel.
Igarashi: In addition to the fresh buzz of a mechanical watch with an enamel dial, the limited-edition model commemorating the 100th anniversary of Seiko watches was in short supply. Even before it went on sale, reservations poured in, and it was sold out immediately. I remember not being able to see the actual watch in the store.
Tomita: In response to this reaction, we made a plan to make the enamel model a regular product, hoping that more people would feel its appeal and be pleased with it.
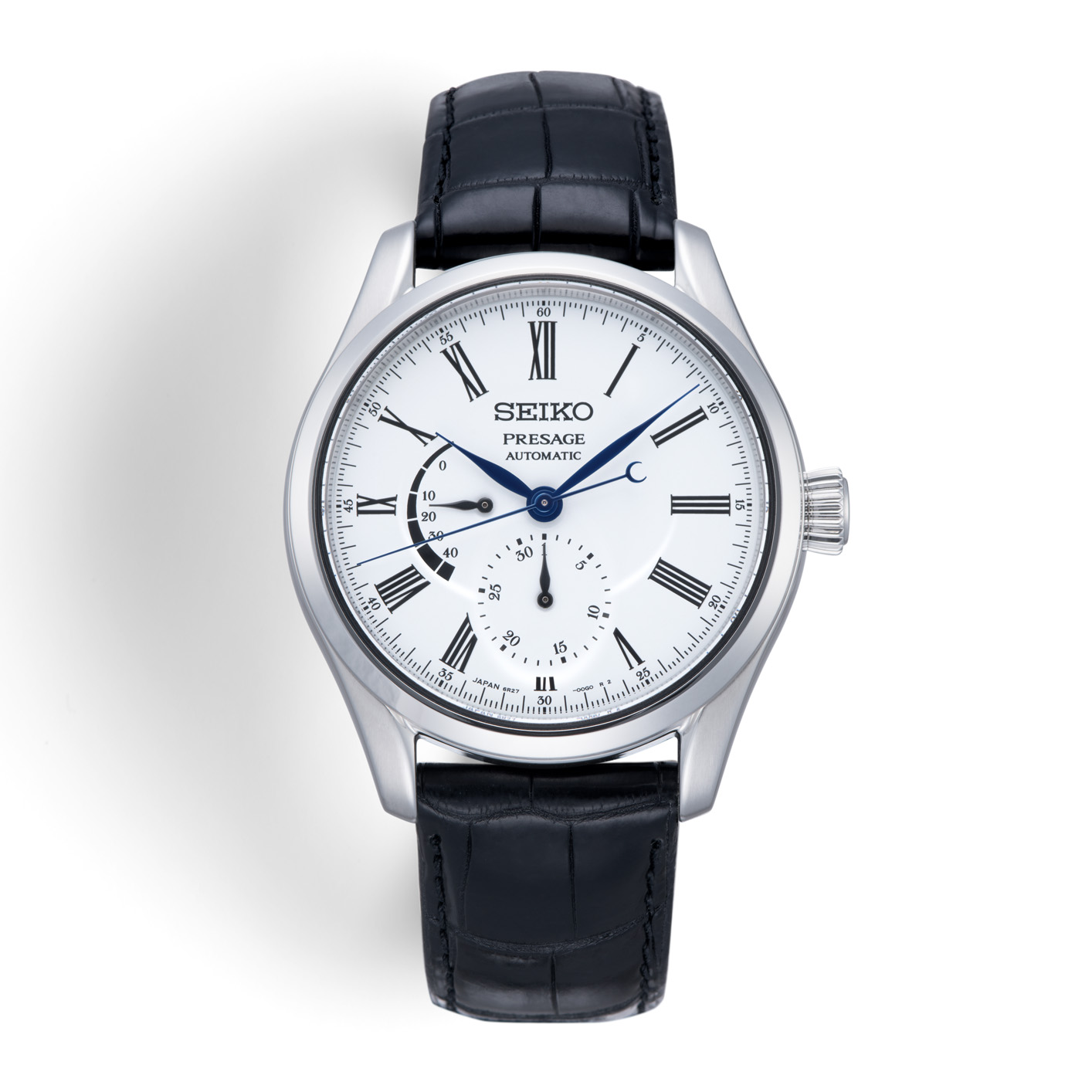
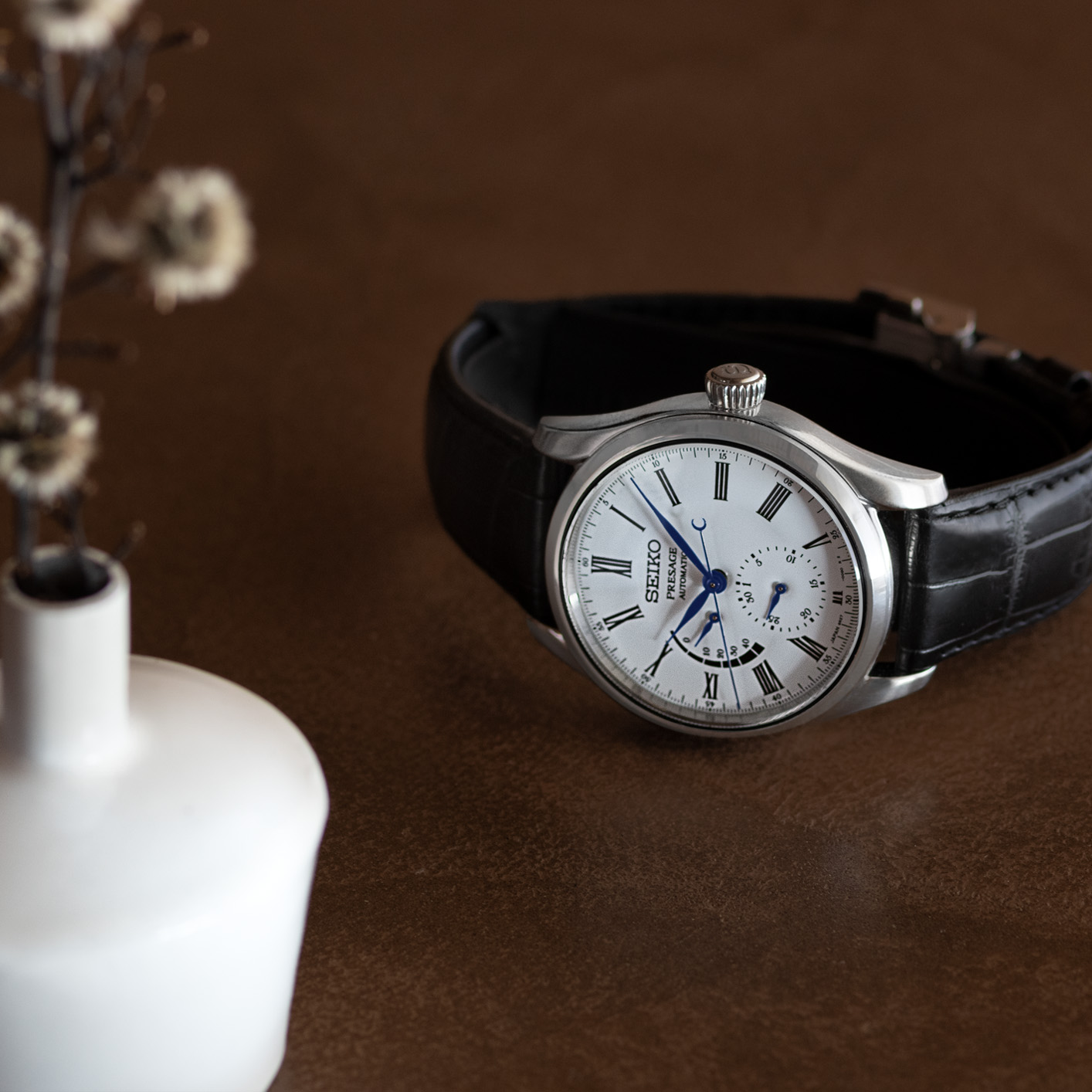
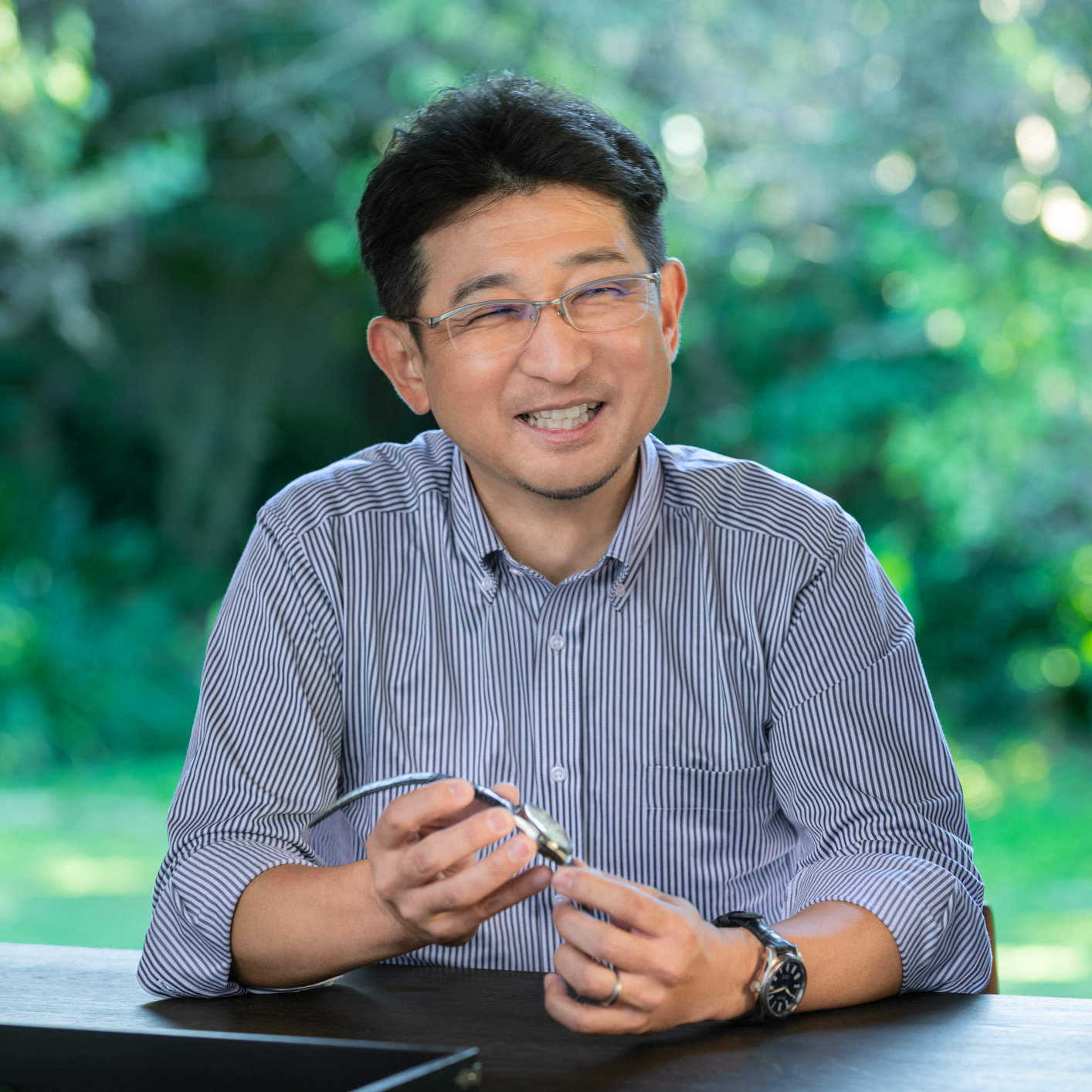
Igarashi joined Seiko in 1989, and since 2001, he was in charge of new model promotion, and he worked with designer Tomita on the development of Presage. Currently, he is working at the watch training center of Seiko Watch Corporation.
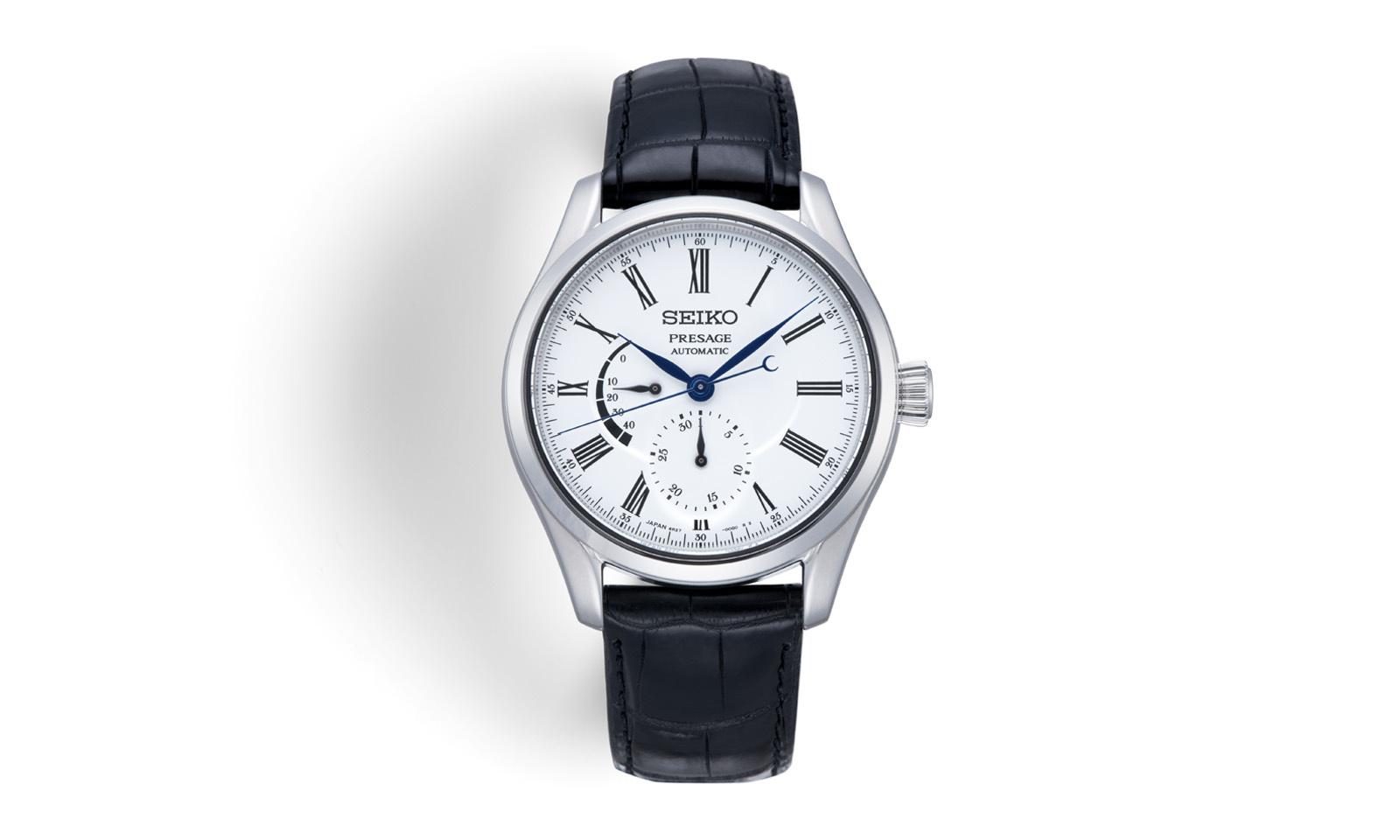
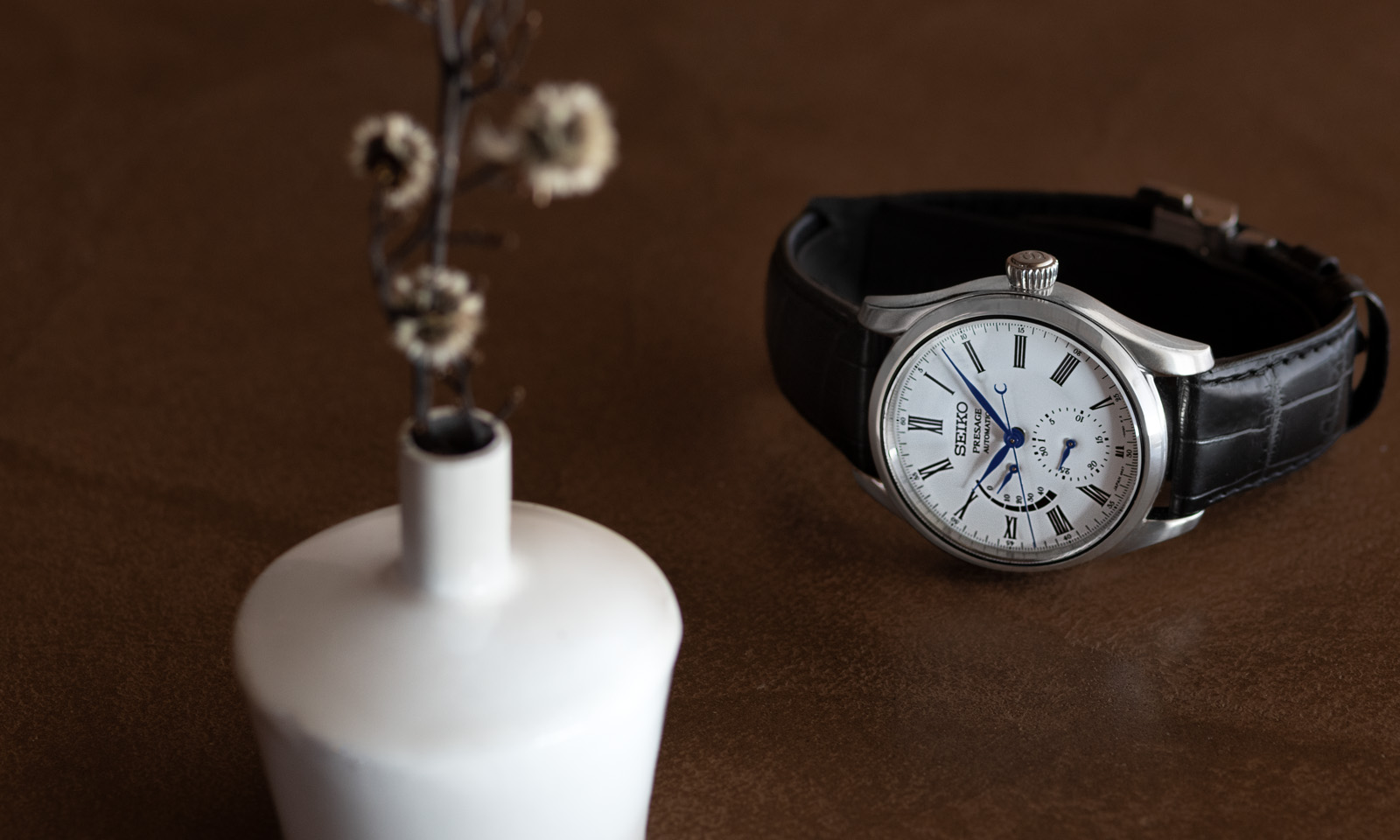
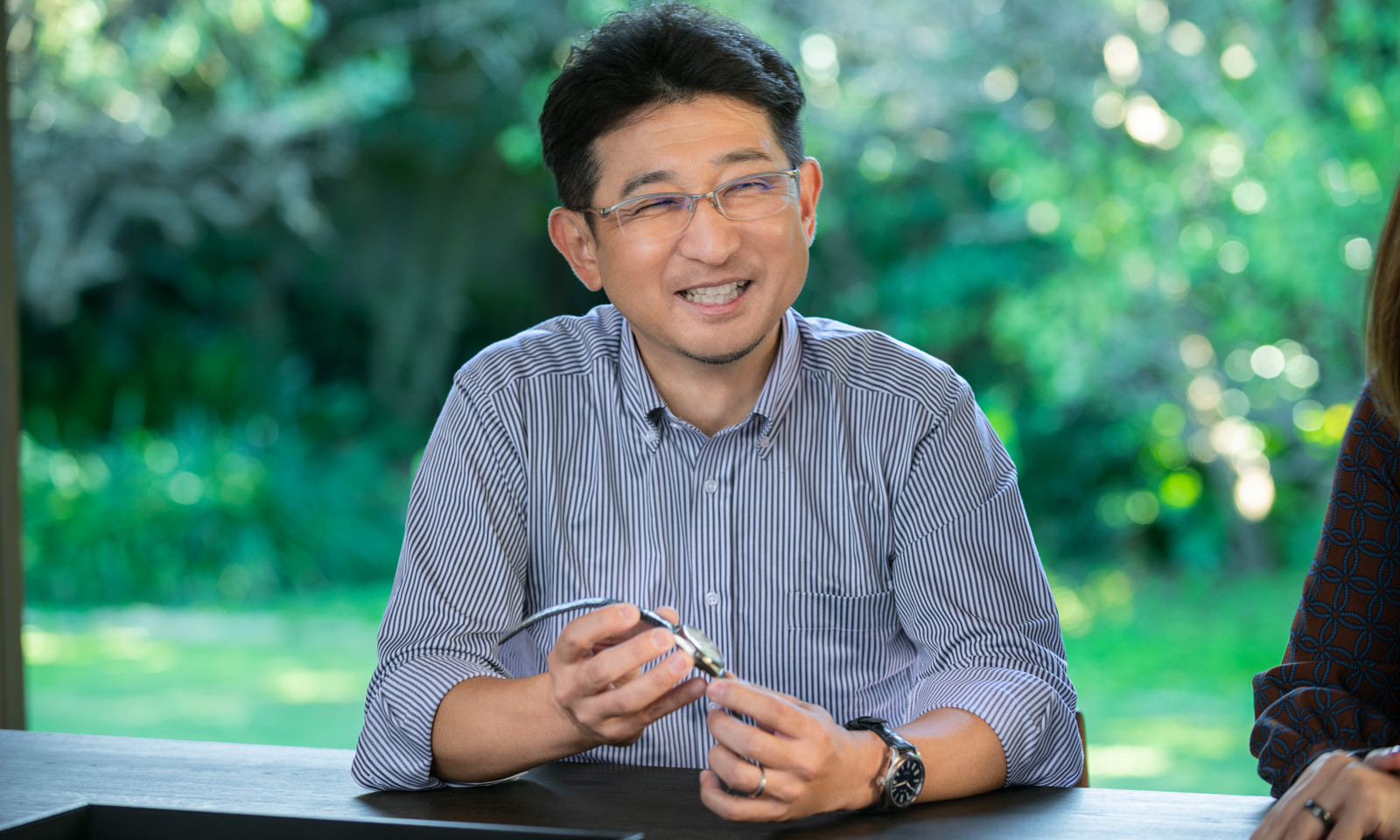
Igarashi joined Seiko in 1989, and since 2001, he was in charge of new model promotion, and he worked with designer Tomita on the development of Presage. Currently, he is working at the watch training center of Seiko Watch Corporation.
The long, hard road to commercialization.
Igarashi: You may think, “What’s so hard about making a product part of the regular line up?” But there is a big difference between making a limited number of dials for a one-time limited edition and continuing to make dials of the same quality all the time. And there were a number of challenges in the enamel production.
Tomita: The biggest challenge was that there was only one craftsman manufacturing the products. Moreover, the number of requests for production had been decreasing, and I heard that he was thinking of retiring soon. However, he is the only one in Japan who can make this enamel dial. Igarashi-san, you provided a lot of support, quality-wise, so that the technique would not be lost, didn’t you?
Igarashi: We had many discussions with the craftsmen and had him repeat the trial production to find out how we could reliably produce a certain number of pieces while maintaining high quality. The baking process of enamelware varies depending on the temperature and humidity of the day, the time of day, and the season, so it is very difficult to adjust the process.
Tomita: I saw a sample that did not bake well, and that helped me understand the great deal of trial and error involved in producing dials that met Seiko’s quality standards.
Igarashi: The fluctuating luster caused by handwork is part of the personality of this enamelware, but how to judge its quality was also a major issue. We had to set up a new standard for judging the appearance of the product, because it is all one-of-a-kind, unlike the way most industrial products are evaluated.
Tomita: In that sense, you could say that we designed a new value of standardizing the beauty of different personalities with enamel. No two pieces are the same, and I think that our customers understand the appeal of this exquisite nuance.
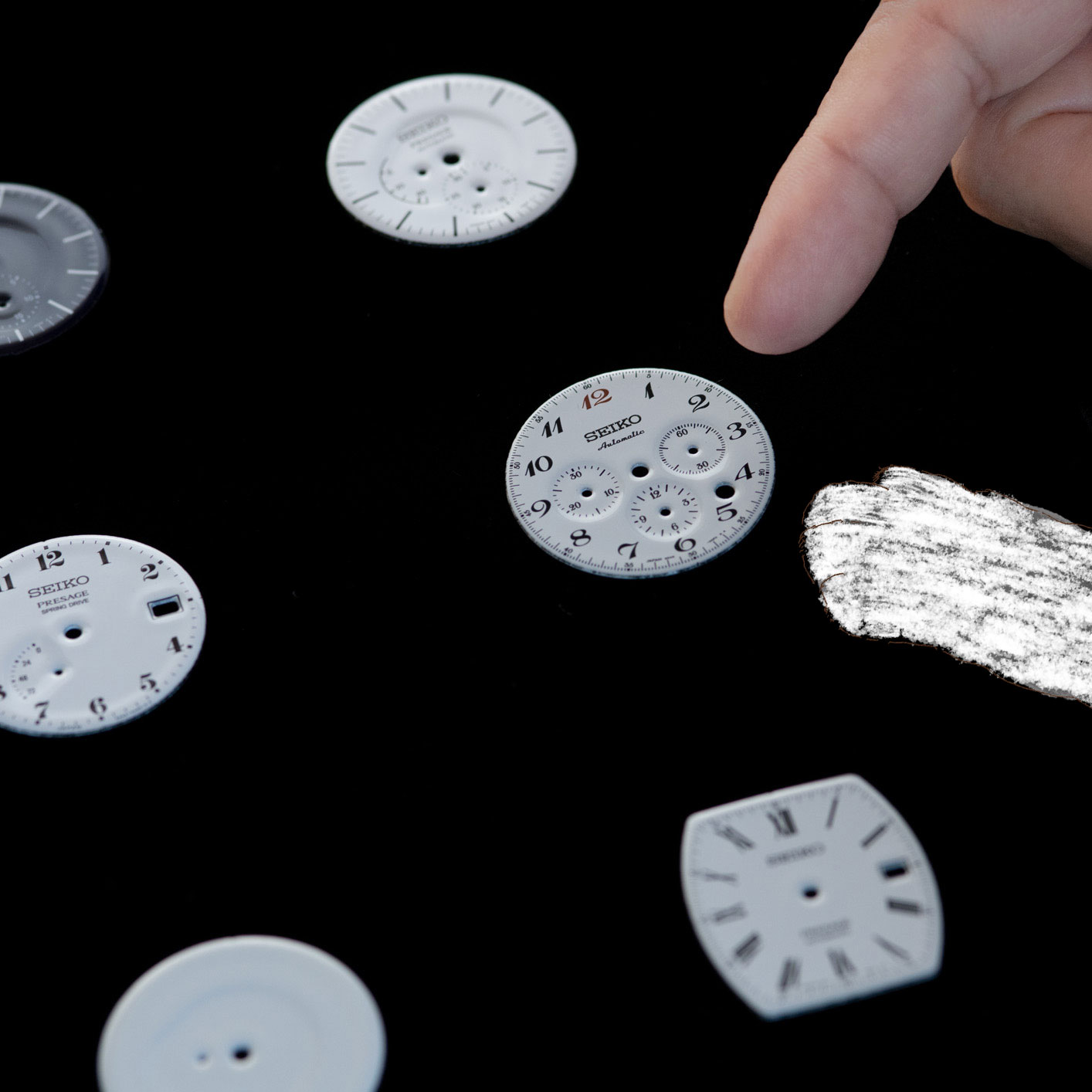
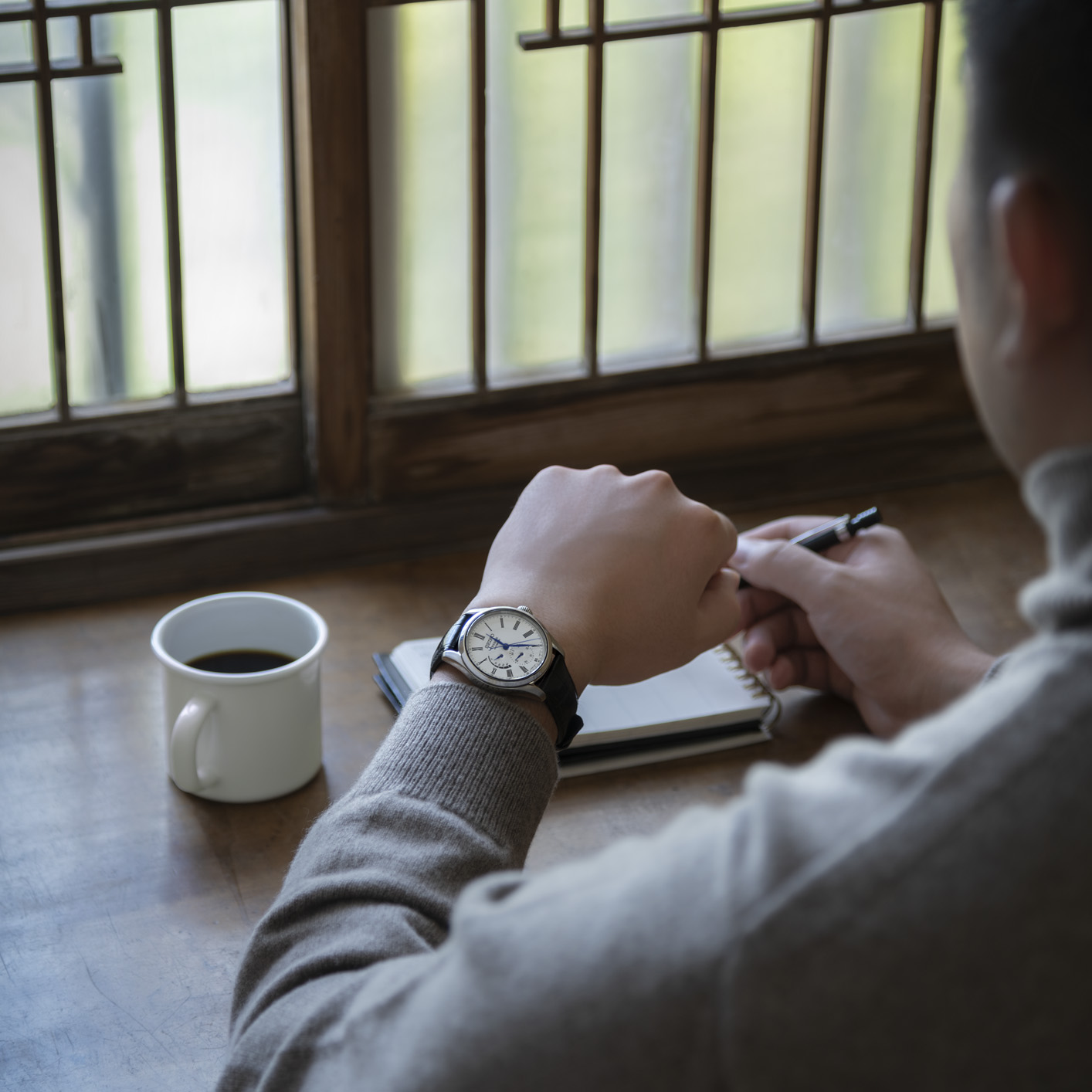
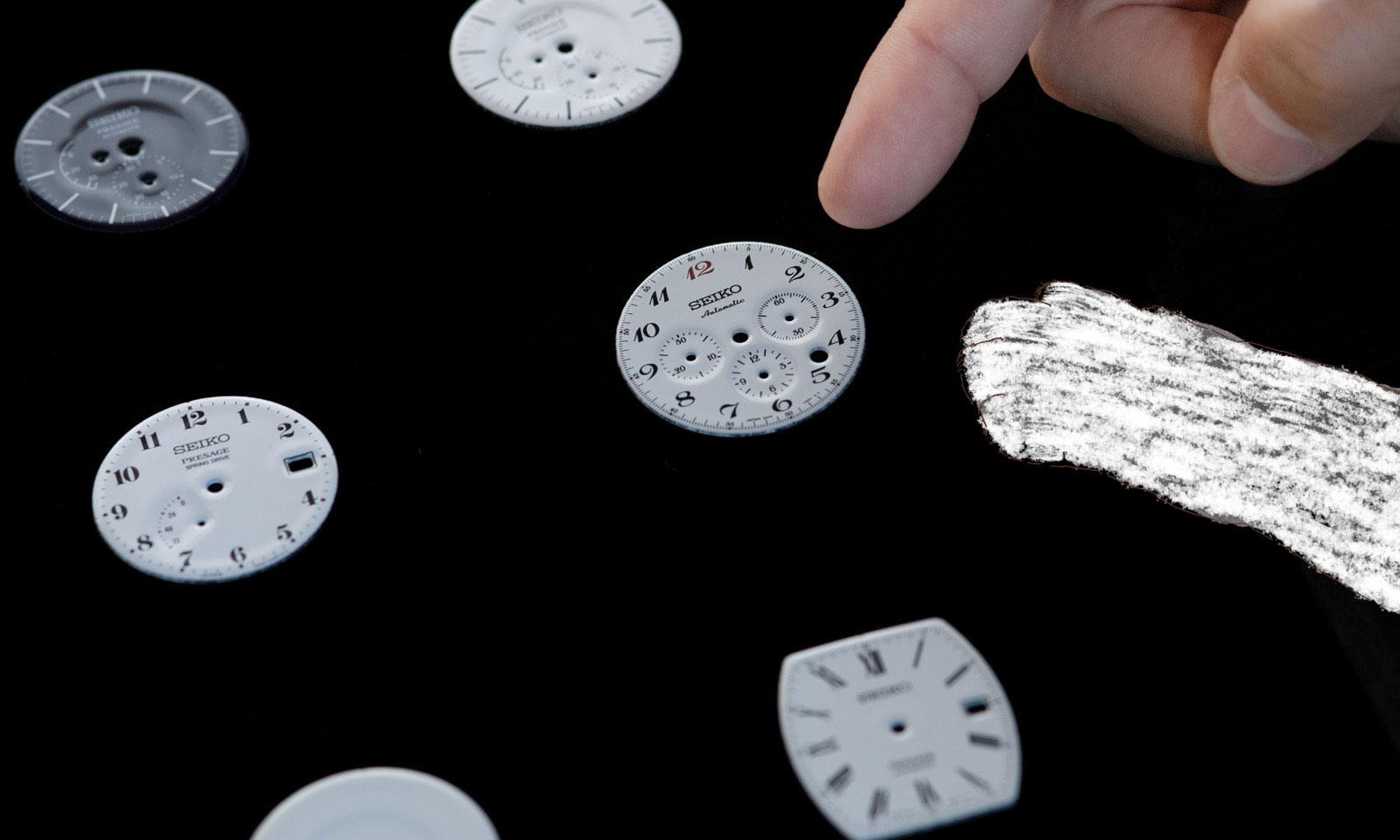
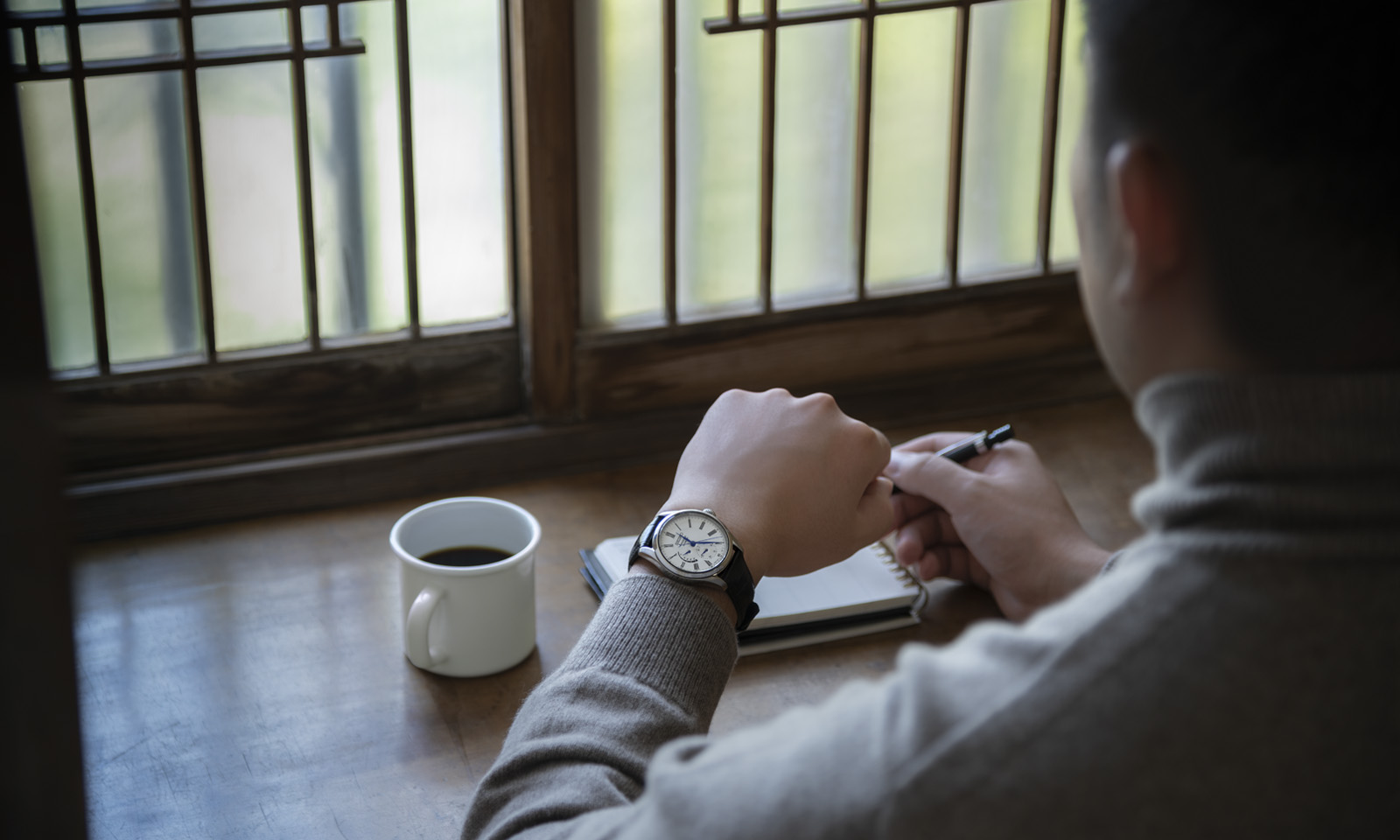
A design that brings out the best of the craftsmanship.
Tomita: After the great response to the enamel dial model, we decided that we could not miss this opportunity to preserve more Japanese traditional techniques and culture, and took on the challenge of utilizing Urushi lacquer in the second model from the Craftsmanship Series. We chose to leave the design more or less the same, aiming for a jet-black color as the counterpart of the unfading white enamel.
Tomita: However, when I designed it, I found it lacking something. I needed to do something to make it feel more like Urushi lacquer. That’s when I came up with the idea of maki-e, a Japanese lacquer technique that uses metal powders, such as gold and silver. Gold powder is often used for maki-e on Urushi lacquerware, and by applying a slightly matte gold color to the hands, we were able to create a very clear and gorgeous impression of Urushi lacquerware.
Igarashi: We also adopted a new printing technology to bring out the appeal of the Urushi lacquer. This allowed us to make the printing of the indexes more raised.
Tomita: This printing technology has the effect of making the watch look very three-dimensional despite its delicacy, and relatively speaking, the Urushi lacquer dial gives the impression of infinite depth as if it draws you in, while the hands and indexes give the illusion of floating. I think I was able to express the appeal that only Urushi lacquer dials can achieve.
Igarashi: As for commercialization, this Urushi lacquer was also made possible by the hard work of the craftsman. For both black and colored Urushi lacquer, it took several months to over a year to achieve the right tone.
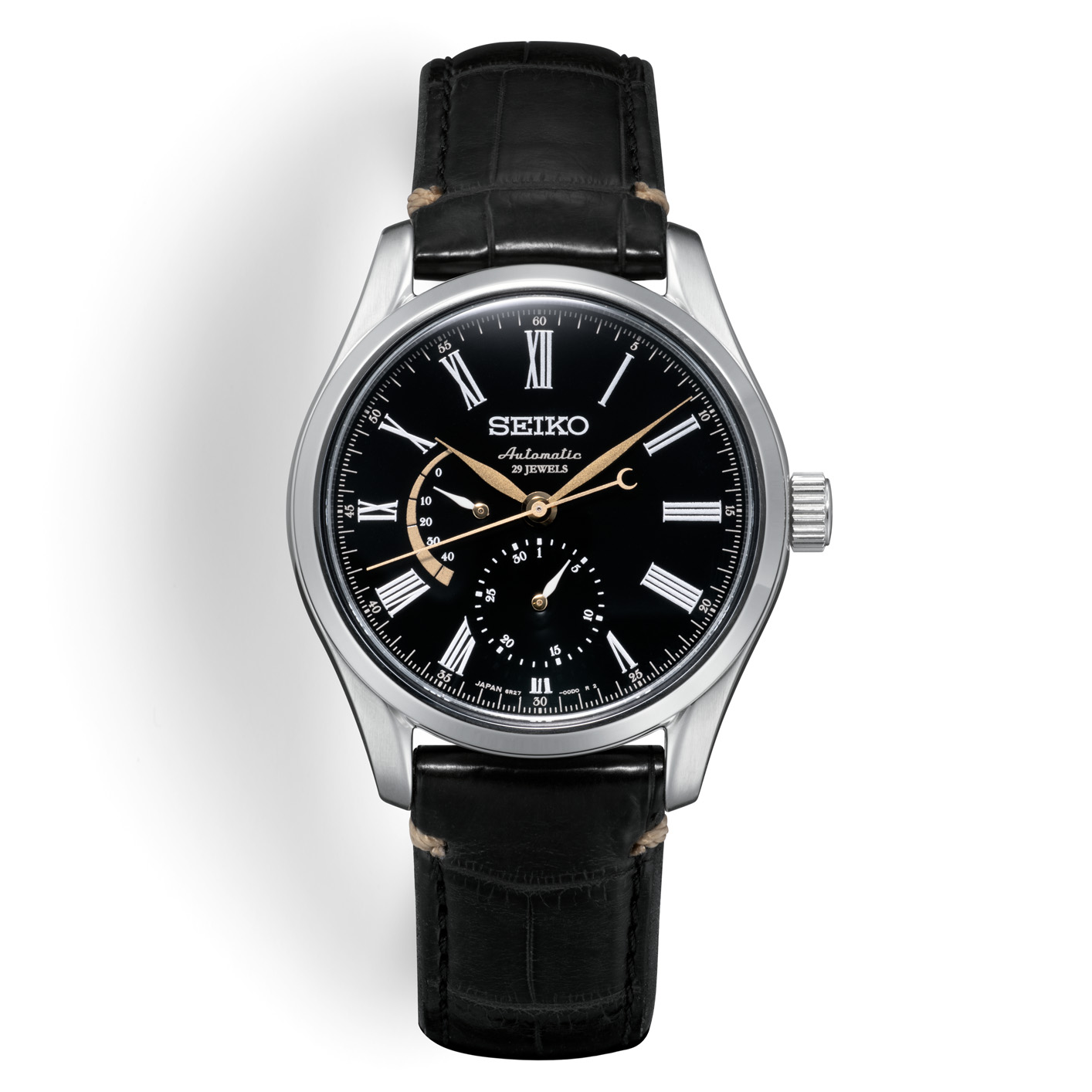
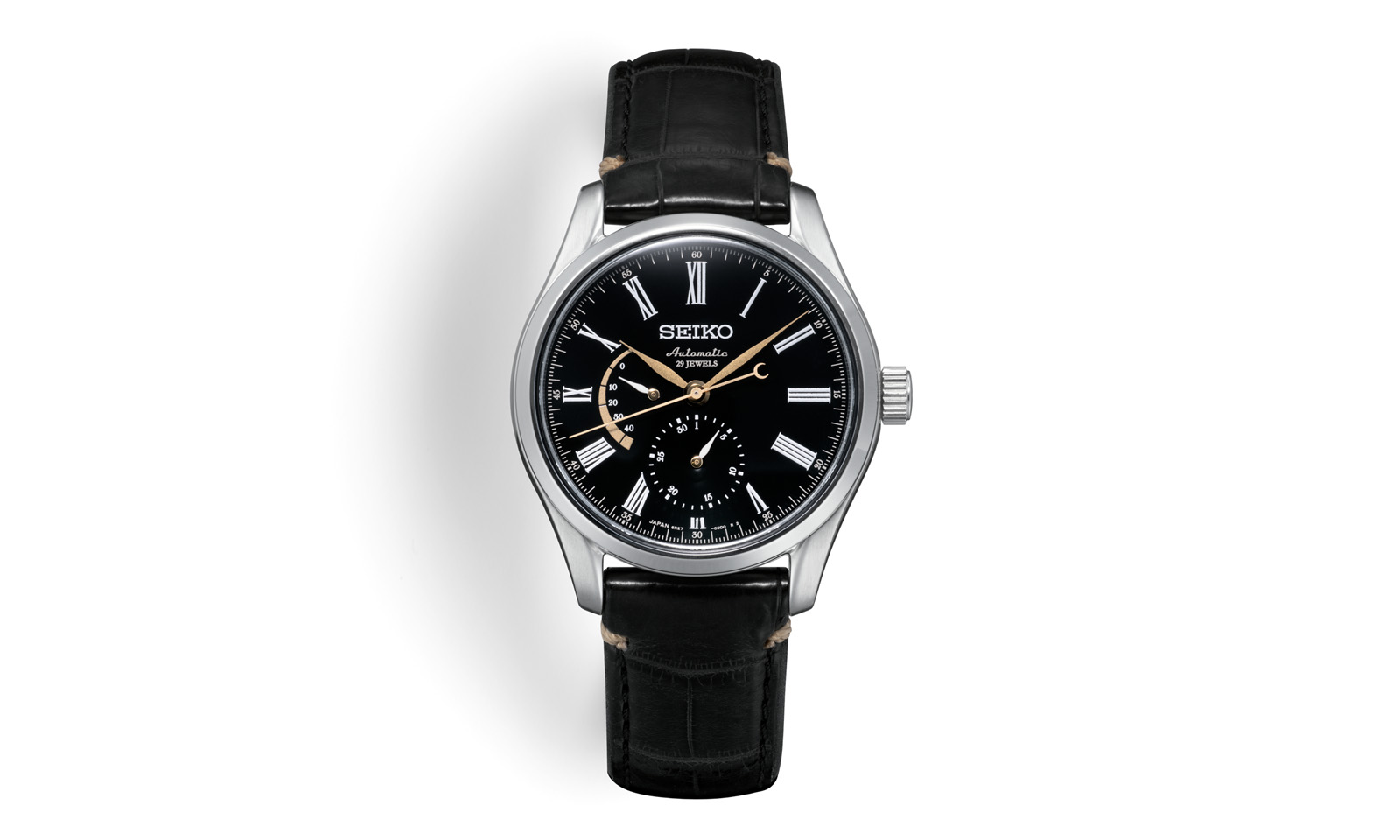
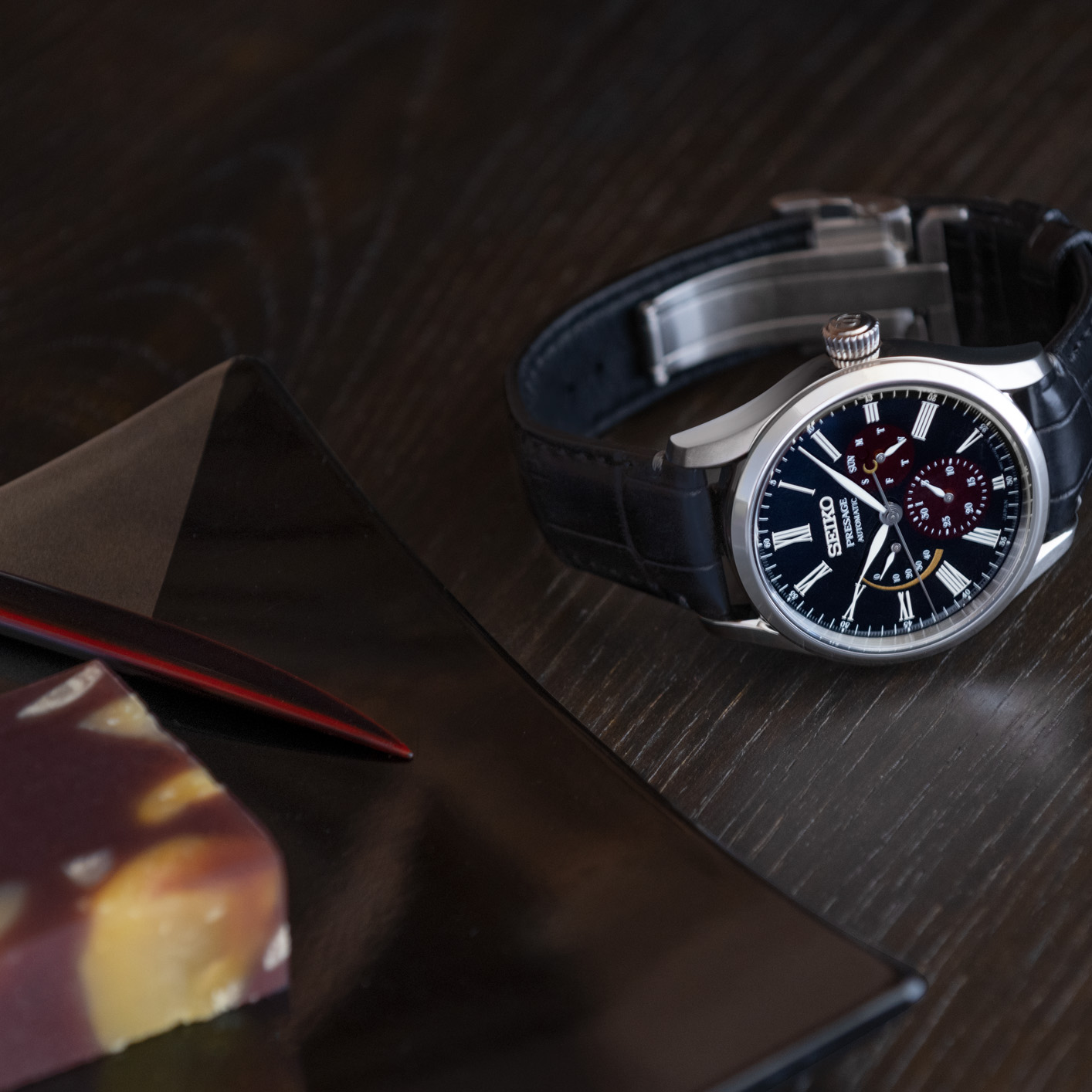
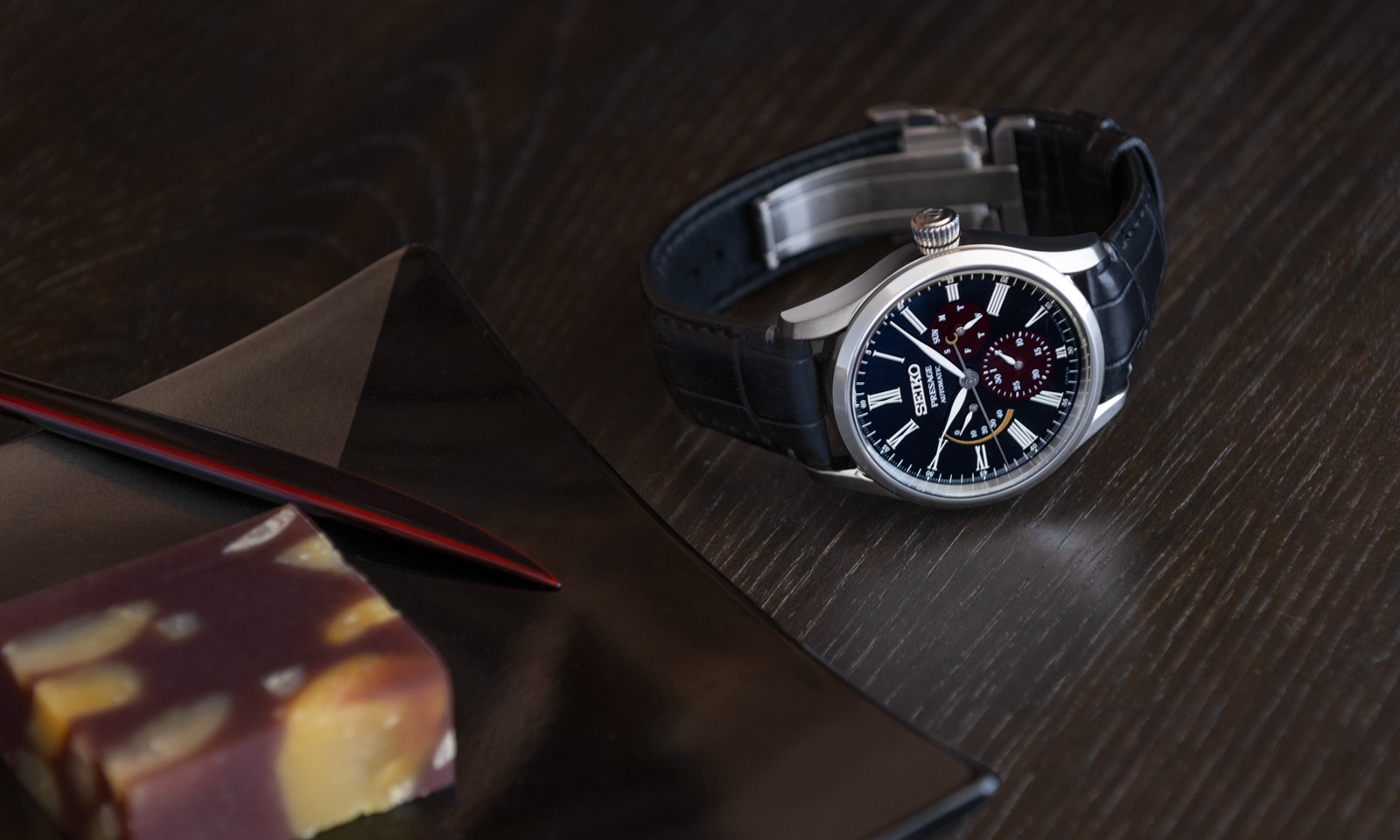
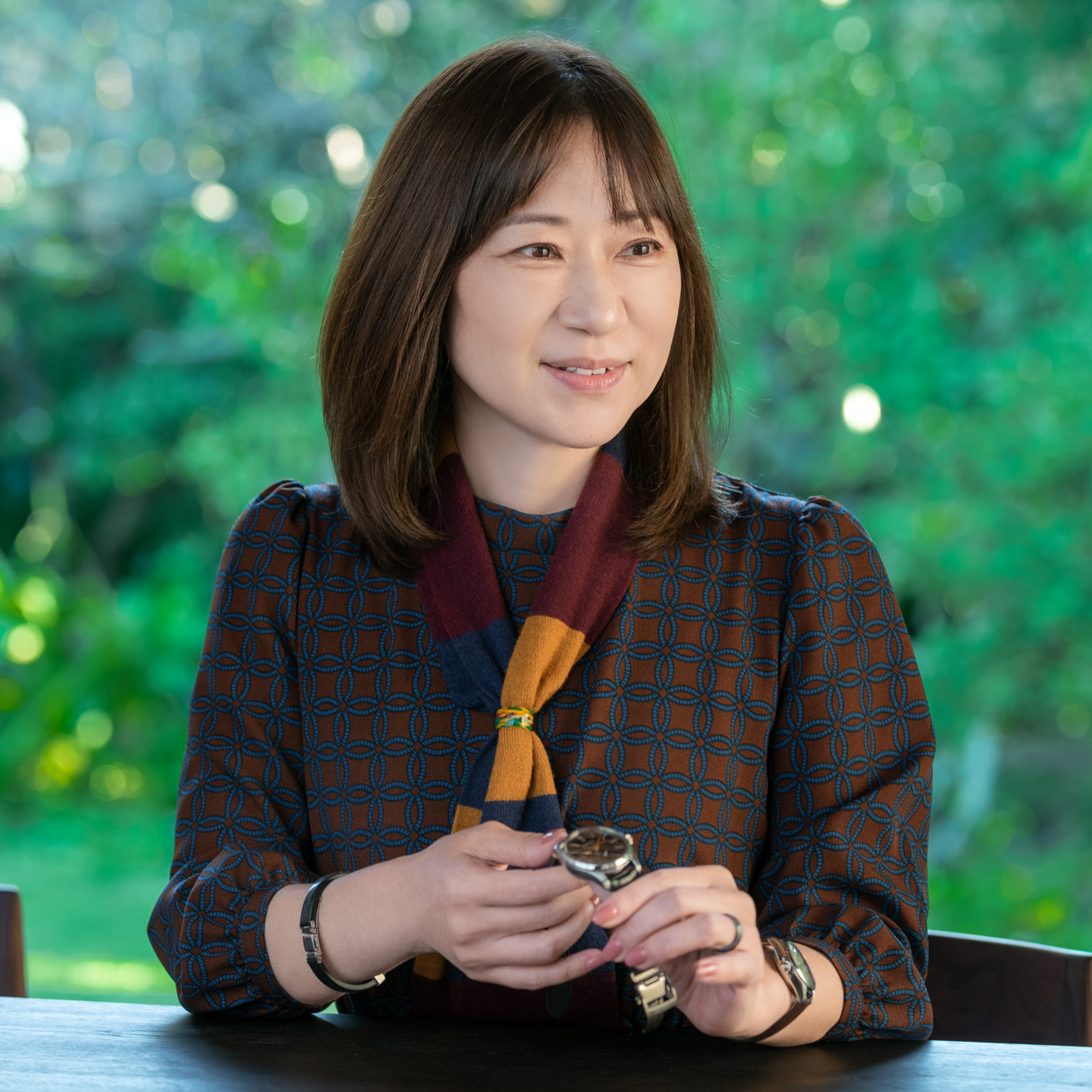
Tomita joined Seiko in 1991. She has been designing a wide range of products for the Japanese market, including LUKIA and the Seiko Moving Design Collection, and has been mainly in charge of Presage since 2011. She has recently been involved in the Re-creation of King Seiko KSK.
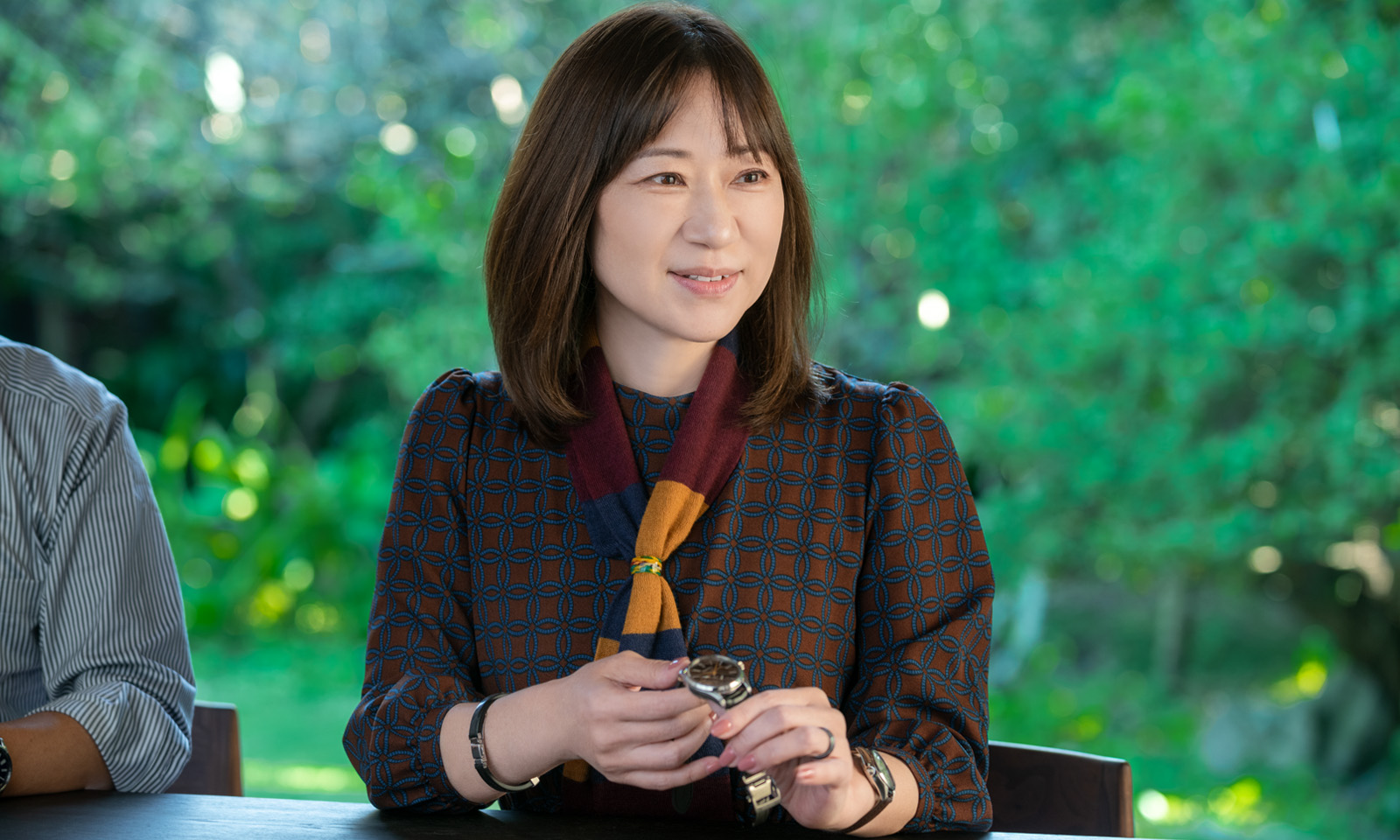
Tomita joined Seiko in 1991. She has been designing a wide range of products for the Japanese market, including LUKIA and the Seiko Moving Design Collection, and has been mainly in charge of Presage since 2011. She has recently been involved in the Re-creation of King Seiko KSK.
Tomita: One of the appeals of Urushi lacquer is its blackness and luster, which gives a sense of depth that makes you want to keep looking at it. It also goes very well with watches.
Igarashi: I think there is more to it than just the appearance. The special feeling of wearing lacquer makes you feel like you are holding your head high.
Wanting to deliver the skills of craftsmen, and to pass it on.
Igarashi: With Tomita-san, we visited the craftsmen’s workshops many times. Did you get a lot of inspiration by visiting the sites?
Tomita: There was a lot to be gained from interacting with the craftsmen. It was challenging to bring back the ideas we discussed and incorporate them into the design.
Igarashi: I felt that a good synergy was created with the craftsmen.
Tomita: That’s right. We were able to create designs that made the craftsmen think, “I want to try this!” and the craftsmen also gave us ideas, so I think we were able to build a good relationship.
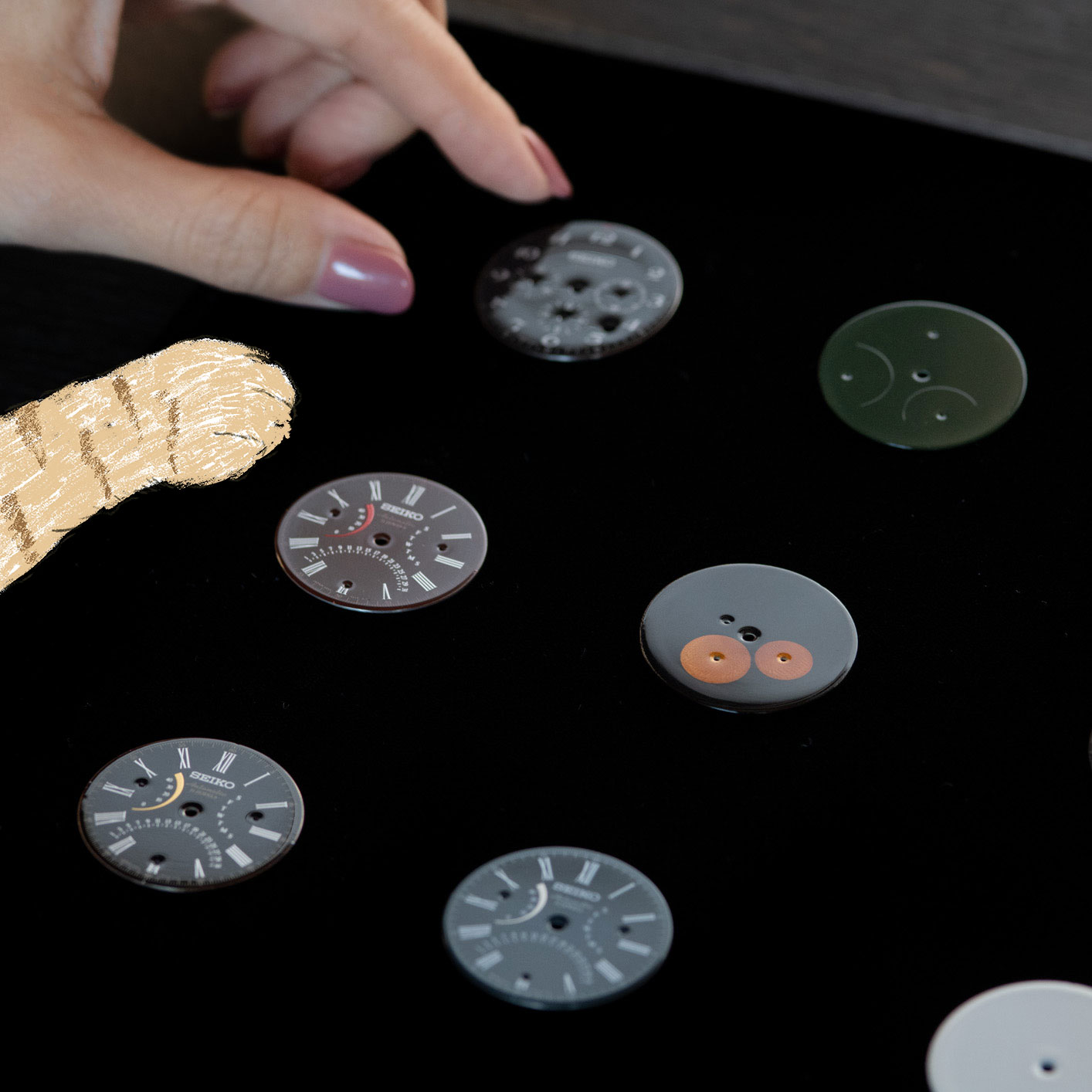
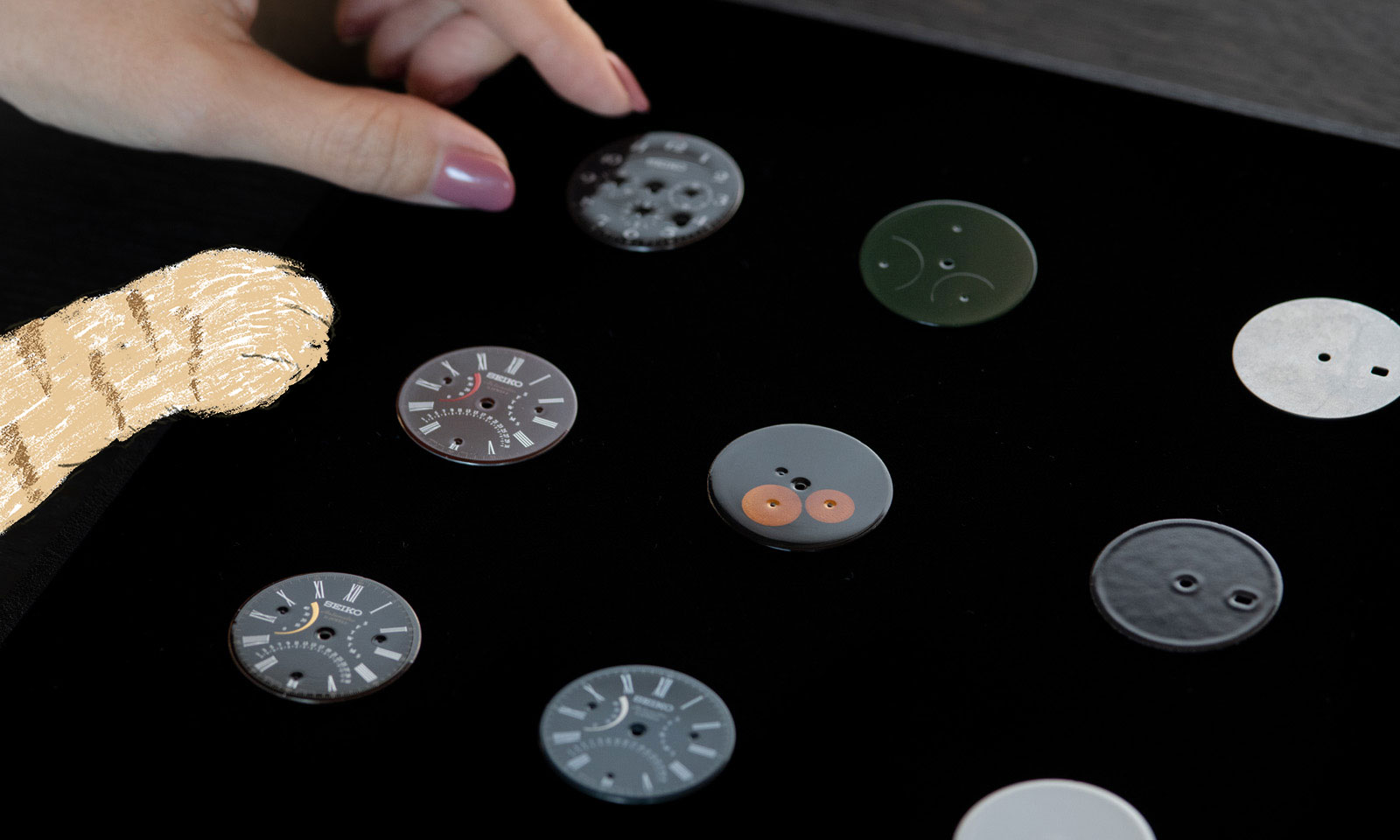
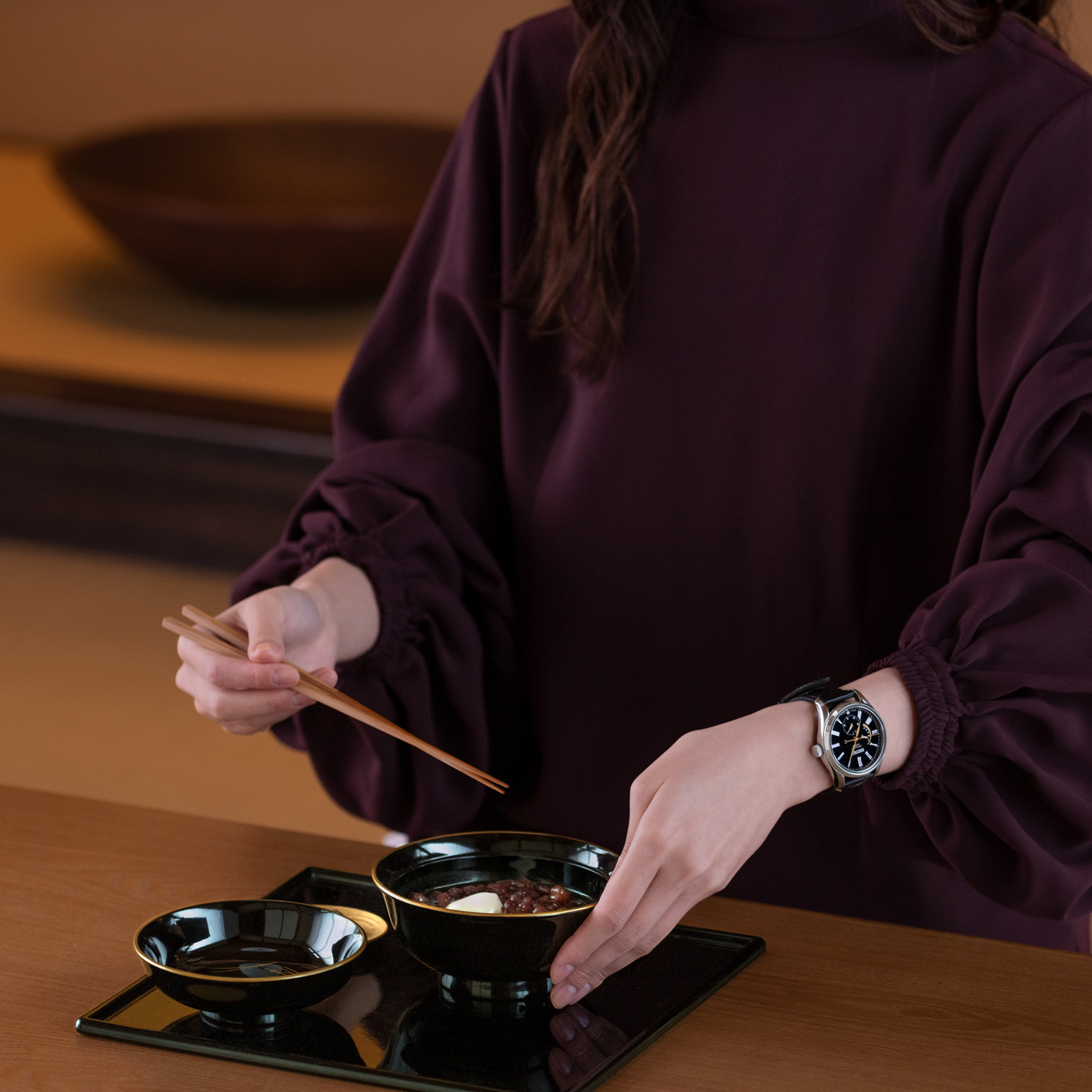

Igarashi: Looking back on it now, I was strongly motivated to respond to the enthusiasm of these two people: the craftsman who pursued the ideal and the designer who tried to express the appeal of the product in the most effective way. However, there were many restrictions and issues that needed to be cleared in order to commercialize the product. I personally came up with ideas and tried to find the best balance so that each of us would be satisfied with the product.
Tomita: In addition to the enamel dial models and Urushi lacquer dial models, we also offer watches with Arita porcelain and Shippo enamel. While each of them has different appeals, what they all have in common when designing is how to bring out the appeal of the material in a simple manner. We believe that maximizing the appeal of traditional craftsmanship as watches will lead to new values.
Igarashi: I don’t think it matters whether it is the watches or craftsmanship that draws someone in, as long as they can understand the value and merits of both mechanical watches and traditional craftsmanship. That is why we try to keep the price as low as possible so that more people can easily pick up our products.
Tomita: My goal is to create a design that will enable Japanese traditional craftsmanship and mechanical watches to become an important part of people’s lives, and that people will always be attached to it. The more you use it, the more you like it, and the more important it becomes to you. I’d like to continue making such watches in the future.
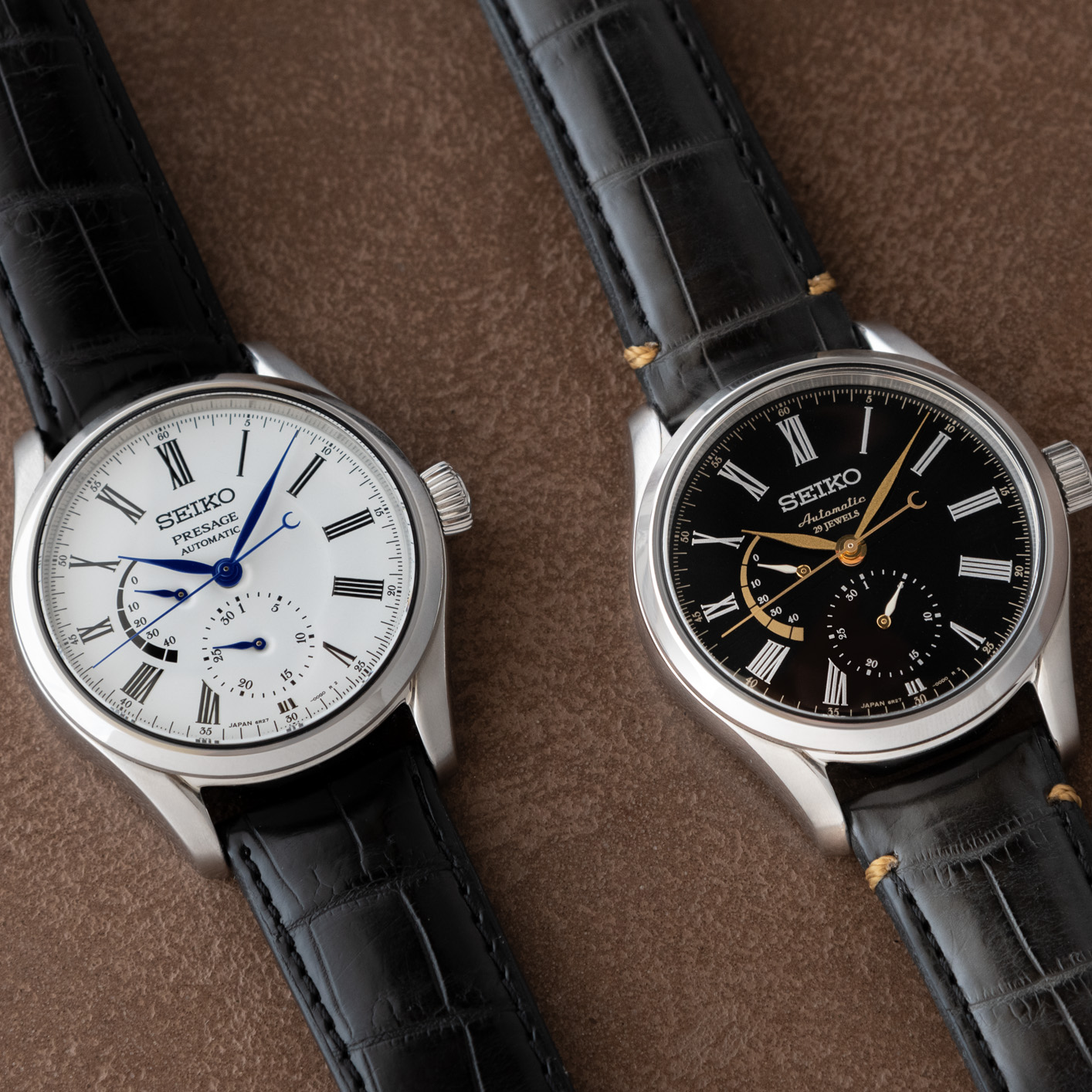
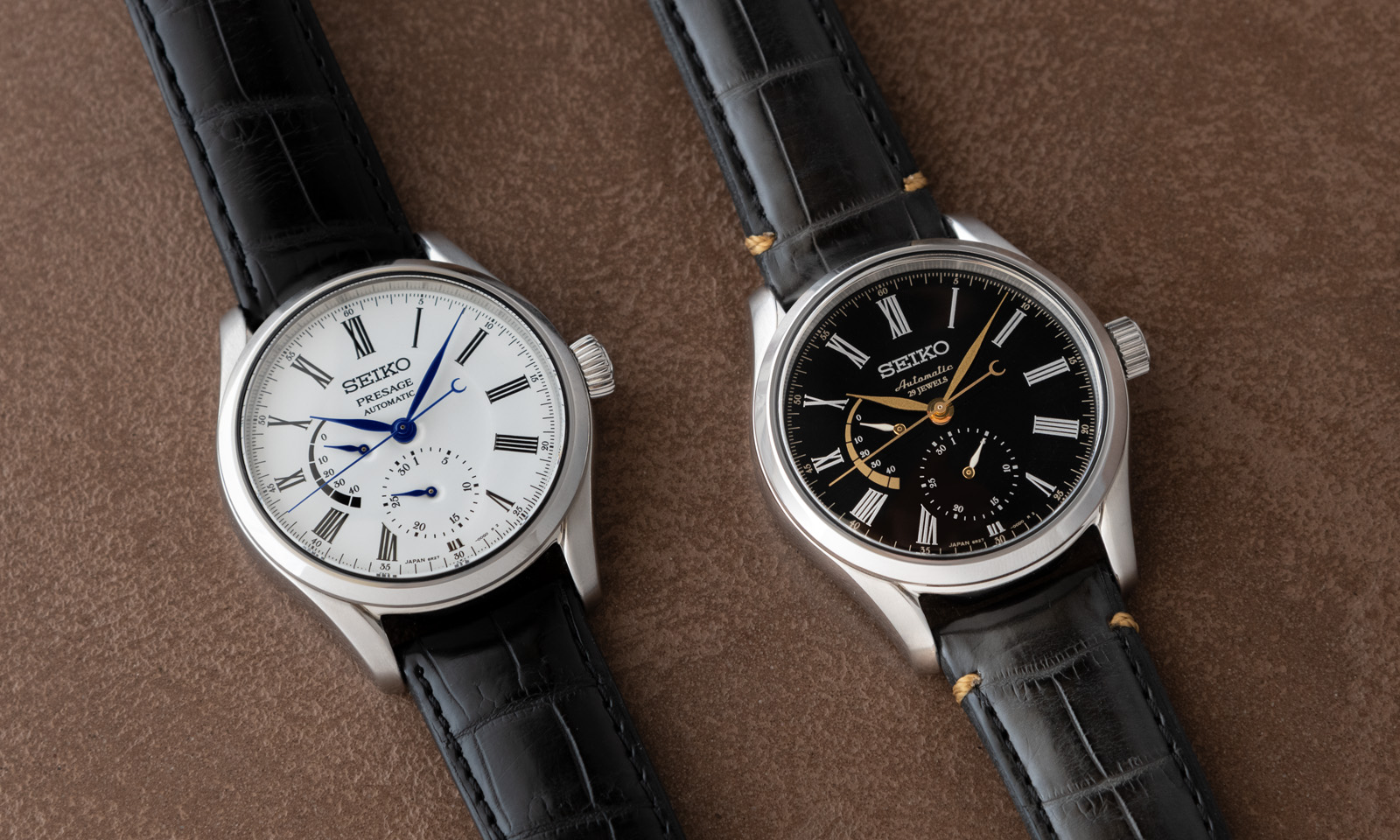